Our products
Precision wear plates for rolling mills
If rolling stands and inserts are equipped with conventional wear plates made of structural steel, tempered tool steel, or bronze, abrasion, impact, and corrosion lead to wear on the guide surfaces, resulting in a reduction in thickness or damage to the wear plates. As surface wear progresses, the clearance between the housing and the insert increases, and the extreme loads are transferred across reduced contact areas – significantly accelerating wear.
In the global market, rolling mills face the challenge of ensuring both the cost-efficiency of the rolling process and the highest quality of the rolled products – which means minimizing wear is essential.
Wear Plates
Precision wear plate made of CORC-g composite steel. Wear is significantly reduced thanks to the hard, abrasion- and corrosion-resistant sliding surface. The base material is unhardened and has a lower strength than the cast material used in the inserts or rolling mill housings. A decisive competitive advantage for any rolling mill.
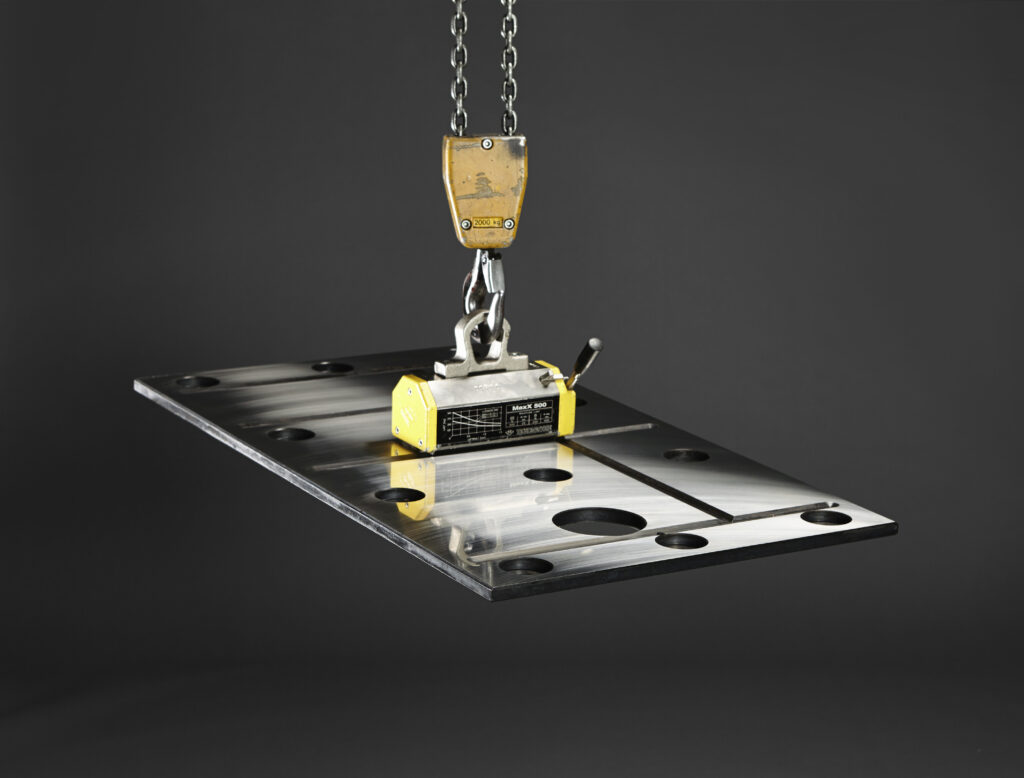
Slide Liners
We know: The manufacturing tool must be more precise than the required precision of the final product. CORTS delivers this level of precision – even for mechanical engineering applications. Based on our customers’ specifications, we produce guide strips made of “CORC-g solid steel” with tolerances in the 0.01 mm range and offer a wide range of material qualities for every application.
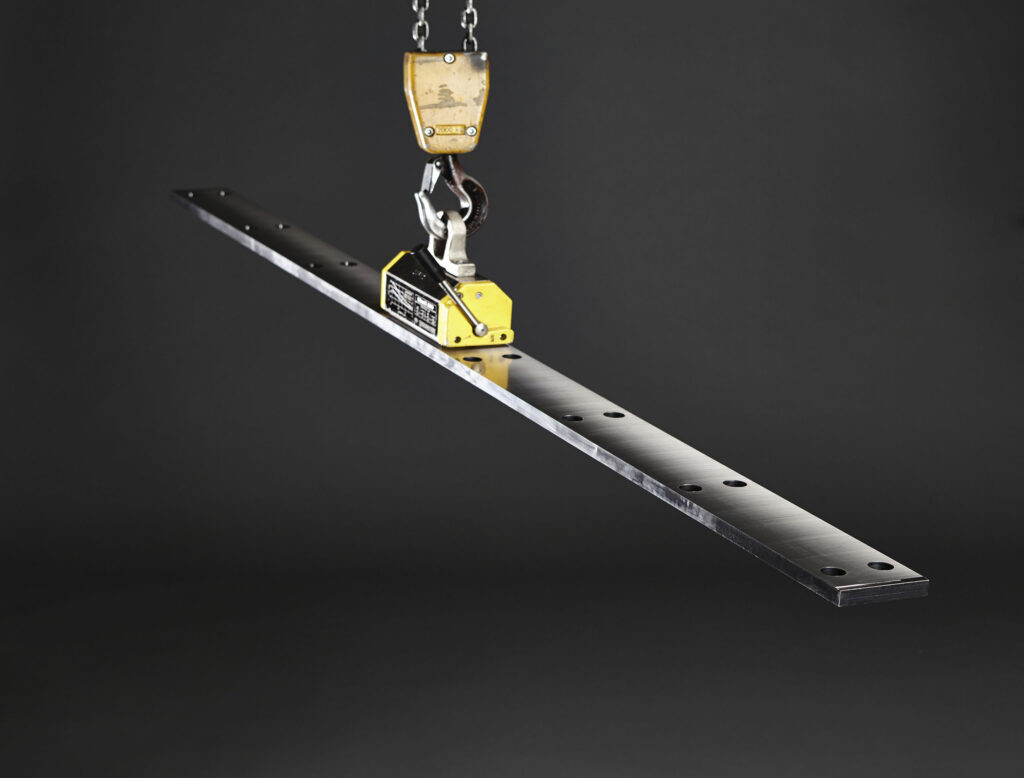
CORC-g Compound Steel
Wear is significantly reduced thanks to the hard sliding surface, which is protected against abrasion and corrosion.
The base material is unhardened and has a lower strength than the cast material used in the inserts or rolling mill housings. This represents a key competitive advantage for any rolling mill.
CORC-g Standard
CORC-g-Standard can be used in almost all application areas and features a very high hardness level in its through-hardened wear layer.
Technical Data:
- 25% through-hardened steel for protection against abrasive wear
- Wear layer hardness: 62 ± 2 HRC
- 75% softer steel to protect the contact surface, e.g., of the rolling mill housing
- Strength of base material: 400–500 N/mm²
CORC-g Stainless
CORC-g-stainless should be used in areas where, in addition to frictional wear, there is significant corrosive exposure. These include, for example, all parts of the plant that come into contact with cooling water.
Technical Data:
- 25% through-hardened stainless steel for protection against abrasive and corrosive wear
- Wear layer hardness: 57 ± 3 HRC
- 75% softer steel to protect the contact surface, e.g., of the rolling mill housing
- Base material strength: 400–500 N/mm²
Dichtleisten für Sinter und Pelletier-Anlagen
CORC-g Extra 90
CORC-g-Extra 90 Used in sintering and pelletizing plants. The goal here is to counteract pure, highly abrasive frictional wear and to achieve maximum plant efficiency. The use of CORTS sinter strips and the guiding principle of “hard against hard” results in up to 8 times the service life compared to conventional standard grades commonly used in sintering and pelletizing operations.
Technical Data:
- 25% through-hardened high-temperature-resistant steel for protection against abrasive wear
- Wear layer hardness: 62 ± 2 HRC
- Excellent high-temperature resistance without tempering effect
- 75% softer steel to protect the mounting surface, with a strength of 400–500 N/mm²
CORC-1000
Pressure-Resistant Components
The enormous pressure in horizontal applications within rolling mills, especially under point or line loads, requires a uniformly tempered or through-hardened structure of the wear plate or strip.
To meet these demanding requirements, we offer the following material grades.
CORC – 1000 qt
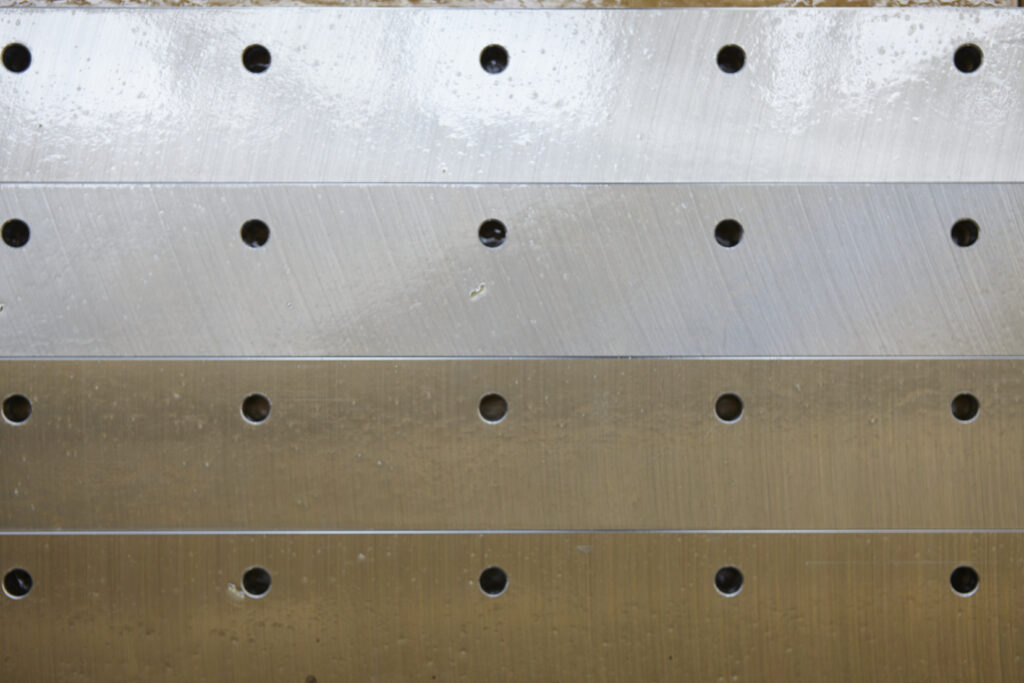
- High-strength tempered tool steel with a tensile strength of 950–1150 N/mm²
- Various hardening processes for additional wear protection
- Also available as a through-hardened version with up to 62 HRC
CORC – 1000 qt inox
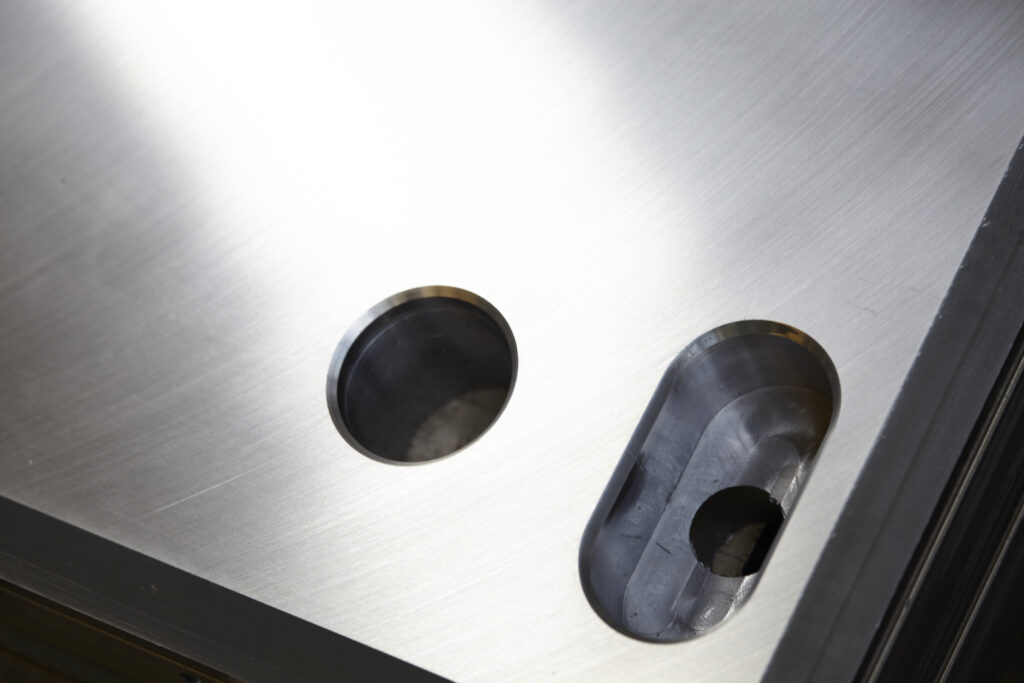
- High-strength tempered stainless tool steel with a tensile strength of 950–1150 N/mm²
- Various hardening processes for additional wear protection
- Also available as a through-hardened version with 58–60 HRC, and up to 62 HRC depending on the material.
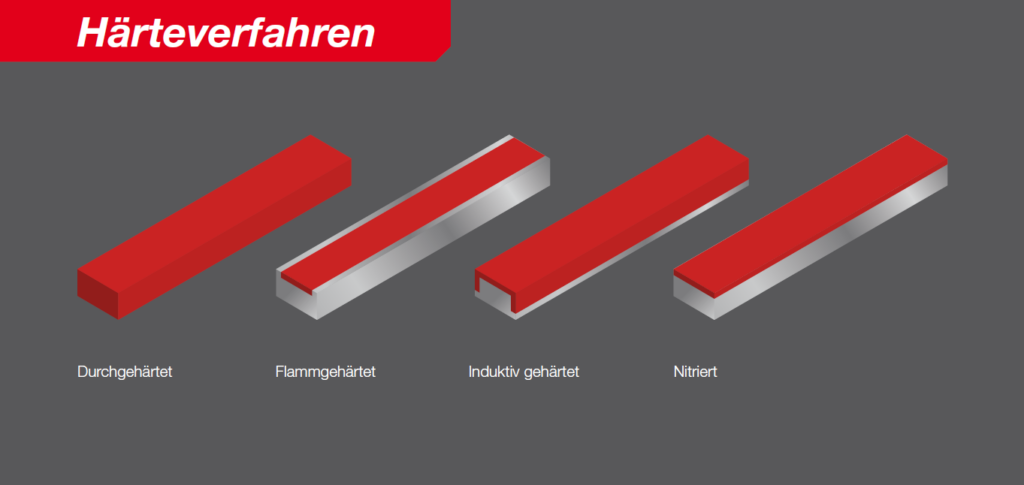
CORC – BR
Bronze strips and bushings
Our philosophy of running two extremely hard surfaces against each other to minimize friction and abrasive wear only works with the use of a suitable lubricant.
However, there are always specific applications where lubrication is either not possible or not permitted.
For this reason, our range of bronze grades completes our portfolio. Our offering includes a variety of classic bronzes as well as aluminum bronzes, with or without graphite inserts for additional lubrication.
An investment that pays off.
The initial investment in our sliding and sealing strips for sintering and pelletizing plants, precision flat guides for rolling mills, and guide strips for mechanical engineering is higher than that of conventional wear parts due to the high material quality and complex manufacturing process.However, in the short and medium term, their use proves to be cost-effective:
With CORTS, you minimize wear, maintenance costs, downtime, and outages – and benefit from lasting precision, optimal production quality, and significantly improved cost-efficiency.